TPU are divided into 2 types: polyester, and polyether.
(A) polyester (heat-resistant, chemical-resistant), polyether (low-temperature resistance, hydrolysis resistance, anti-bacterial)
(B) high strength, wear resistance, weather resistance, environmental protection, non-toxic, easy to recycle decomposition, resistance to bending and disturbance.
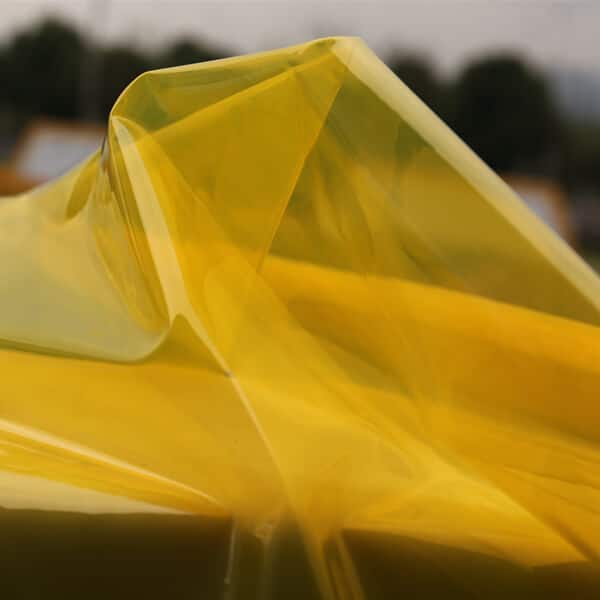
1. Hardness–ASTM D-2240
TPU hardness is usually determined by Shore A (Shore A) and Shore D (shore D) hardness tester, Shore A for softer TPU, Shore D for harder TPU. hardness is mainly determined by the hard segment content in TPU structure, the higher the hard segment content, TPU hardness will rise. As hardness increases, other properties of TPU also change. tensile modulus and tear strength increase, rigidity and compressive stress (load capacity) increase, elongation decreases, density and dynamic heat generation increase, and environmental resistance increases. hardness of TPU has a relationship with temperature. There is no significant change in hardness when cooling down from room temperature to abrupt change temperature (-4~-12℃); at abrupt change temperature, TPU hardness suddenly increases and becomes hard and loses elasticity as a result of the crystallization of soft segments.
The relationship between hardness and constant tensile stress and elongation and the relationship between hardness and tear strength. As the hardness of TPU increases, the 100% constant tensile stress and 300% constant tensile stress increase rapidly and elongation decreases. This is mainly due to the increase in hardness content: the higher the hardness content, the easier it is for the hard phase to form secondary crystals or crystalline structures increasing the amount of physical cross-linking and limiting material deformation. The relationship between TPU hardness and tear strength, with the increase in hardness, tear strength increases rapidly, the reason is the same as the explanation of modulus.
2. Tensile strength–ASTMD412
In the tensile test, the specimen until fracture by the maximum tensile stress is the tensile strength, the results are expressed in MPa. Some incorrectly called tensile strength, tensile strength, etc. Tensile strength 28.3 to 62MPa, ester type is higher, ether type is lower.
3. Elongation at break (elasticity, toughness)—ASTMD412
Elongation at break is the percentage of increase in the length of the effective marked part (between the two jigs) when the film is stretched and the length of the initial effective marked part (between the two jigs), and elongation at break is a measure of toughness (elasticity) index.
With a large elongation at break, characterized by a certain unisex elongation of the measured object against impact, will not immediately brittle break.
4. Tear strength —- ASTM D412
Elastomer in the application of the crack to expand the damage for the tear, and the tear strength is to evaluate the price of the ability of the material to resist the tearing effect. For general film materials, often the longitudinal and transverse properties are different, so the sample should be measured separately.
5. Modulus of elasticity
The macro mechanical properties of the material at room temperature and under static load. It is the main basis for determining various engineering design parameters. These mechanical properties are required to use standard specimens on the material testing machine in accordance with the prescribed test methods and procedures, and can be measured at the same time the material stress-strain curve. 300% of the TPU material constant tensile modulus of 7.6 to 33 SMPa.
6. Abrasion resistance
When the material is often subject to friction, scraping, erosion and other mechanical effects caused by the gradual wear of the material surface. The wear rate or the reciprocal of the wear degree under the specified friction conditions is expressed. It is related to the hardness of the film itself.
7. Bending resistance
When the product needs to be used under repeated cyclic stress, it is necessary to pay attention to the case of fracture due to poor flexural resistance of the material.
8. Yellowing resistance/UV resistance —ASTM G154
- TPU material in the general environment, exposure to ultraviolet light, oxygen, etc., aging phenomenon, resulting in product performance decline and surface yellowing phenomenon.
- Yellowing resistance test reference.
- The addition of stabilizers and absorbers can also delay the photo-oxidation process of aromatics, but not to the same extent as aliphatics. Experimentally compared to the gray card, divided into 1-5 levels. After the yellowing resistance test such as Suntest, QUV, or other sunlight tests, compare the color change of the samples before and after the test, the best grade is 5, representing basically no color change. 3 below is an obvious color change.
Generally speaking grade 4-5, which is slight discoloration, is sufficient for most TPU applications. If you need no discoloration at all, you need to use aliphatic TPU, which is the so-called non-yellowing TPU, the base material is not MDI, generally HDI or H12MDI, etc., long time UV test will not change color.
Aging guarantee about 2-3 years, and the use of environmental related.
9. Hydrolysis resistance
TPU has good hydrolysis resistance in turbid water, and no obvious hydrolysis will occur within 1-2 years, especially in polyether series. Polyester series is easy to absorb moisture, soak in 50℃ water for half a year or 70℃ for 3 weeks or 100℃ for 3-4 days, it will be completely decomposed. It needs to be stored at dry room temperature.
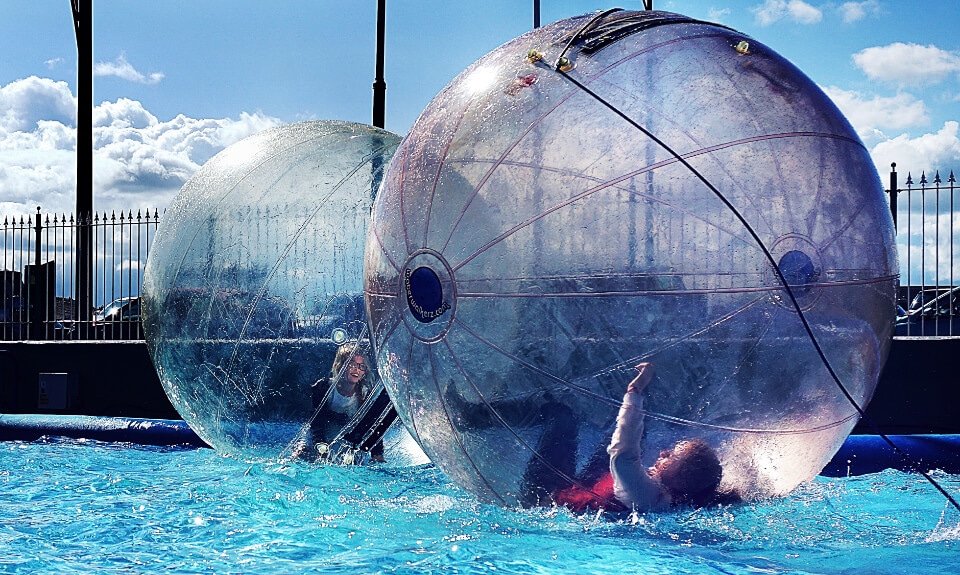
10. Oil and drug-resistant performance
An extremely polar polymer material and non-polar mineral oil has little affinity. In fuel oil (such as kerosene, gasoline) and mechanical oil (such as hydraulic oil, oil lubricating oil, etc.) is almost not subject to erosion, polyester series oil resistance is better, the volume change for grease is very small, the tensile strength is even higher than the original initial value, compared to other material properties reduced and more obvious excellent, it should be noted that if the mineral oil contains a small amount of water, will have different degrees of negative impact on the film properties.
11. Heat and oxidation resistance
When the product needs to be used in high temperature (such as 70 degrees) or above for a long time, the oxidation (aging) of the selected material and the oxygen in the air must be considered, the film can cope with various harsh environments, and the general temperature resistance is about 130 degrees or above. Polyester heat resistance is better.
12. Low temperature performance
The film has very good low-temperature resistance generally can reach -30 degrees Celsius, which can replace the use of general PVC will be brittle. It is suitable for products related to cold zone. Polyether is better for cold resistance.
13. Anti-mold and anti-bacterial performance
The film has better anti-mold and anti-bacterial property, can resist Penicillium, Aspergillus, short-stalked mold, mixed bacterium and other microorganisms, etc.
14. Gas diffusion performance (airtightness)
The film is very easy to use high modulation wave or hot pressing to fuse, so it is widely used in blowing (filling) gas products, gas diffusion coefficient refers to the diffusion rate of gas through the specified area of the specimen at a certain temperature and pressure, the same material to different gas penetration rate sometimes varies greatly, polyester series products have better gas tightness than polyether series.
15. Biomedical performance
The film has excellent biocompatibility, non-toxic, non-allergic, non-local irritation, non-pyrogenic, so it is widely used in medical, health and other related products and sports protection equipment.
16. Waterproof and moisture permeable
Unlike microporous film, TPU belongs to hydrophilic film, which is composed of single-component copolymer, consisting of hard and soft chain segments arranged alternately along the macromolecular chain. The hard chain segments are hydrophobic, which can prevent water droplets from passing through and play a waterproof role; the soft chain segments are hydrophilic, which can act with water molecules and adsorb water molecules on the high humidity side with the help of hydrogen bonds and other intermolecular forces, and desorb them on the low humidity side through the transfer of hydrophilic groups on the polymer chain, thus achieving the effect of moisture permeability. The process of moisture permeability is also known as “adsorption – diffusion – desorption”.
17. Corona treatment
It makes the surface of the substrate have a higher adhesion.
Corona treatment is time-sensitive, and the treatment effect will decline to different degrees with the type of film, humidity of storage environment and storage time.
18. Film surface antistatic treatment
When two physical state of different solid contact friction, their respective surfaces will occur charge redistribution, after re-separation, each solid surface will carry an excess of positive (or negative) charge than before contact, this phenomenon is called static electricity. The way to remove static electricity is generally to use surfactants, such as antistatic agents to reduce the surface resistance of the polymer. As such additives are hygroscopic, a very thin conductive film is formed on the surface of the polymer by absorbing moisture from the atmosphere, thus enabling the rapid elimination of static electricity. Moisture plays an important role in this process, and as the atmospheric humidity increases, the surface conductivity of the polymer also increases, resulting in a rapid loss of electrostatic charge and producing better antistatic properties.
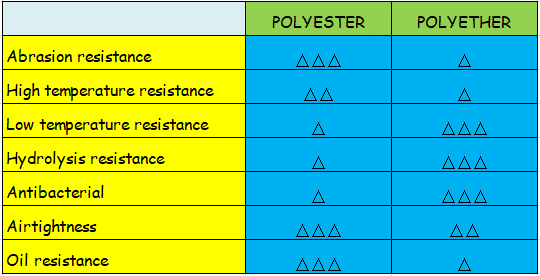